What is a high frequency wave? Many people have questions and don't know how to answer this question.
In fact, high-frequency waves are a kind of ultrasonic waves, and their distinguishing standard is frequency. When the frequency of the ultrasonic wave is greater than 100 kHz, we call it a high frequency wave. The high-frequency wave uses the principle of frictional heat generation to generate a large amount of heat for the purpose of welding and welding. For example, the high-frequency wave plastic welding machine that we often encounter uses the huge energy generated suddenly to weld the target object.
High-frequency plastic welding machine (referred to as high-frequency machine, English Hing freguency plastIC wELDer), is the electronic tube to convert electrical energy into electromagnetic waves, after oscillation into a high-frequency electromagnetic field, and then transfer the high frequency to the cookware through various transmission paths (upper pole ), PVC tape between the cookware and the ground (that is, the upper and lower poles of the high-frequency electromagnetic field), the polarization of the plastic polar molecules is vigorously moved to generate heat. The tape reaches the effect of fusion setting under mold pressure.
The key technology of high frequency machines is to generate high frequency electromagnetic fields. The vacuum tube of the fusion splicer converts high-voltage electrical energy into electromagnetic energy, and oscillates through the oscillating barrel to generate a high-frequency electromagnetic field. The oscillation frequency of the oscillating barrel directly affects the strength of the output force, which in turn affects the welding quality of the product. How to determine the oscillation frequency and then adjust to the appropriate size becomes critical. In today's mechanized and digitalized, the adjustment of the oscillation frequency of high-frequency plastic welding machines is still regulated by the experience of workers. This manual adjustment often leads to defects or even failures in the welding of the product, and the production cost rises. Therefore, using an electronic instrument to measure the optimal oscillation frequency is the best way to solve this problem.
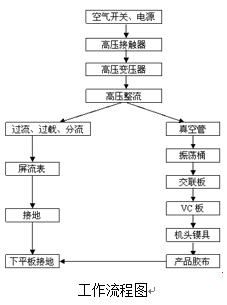
Since the electromagnetic energy oscillation is after boosting, the voltage at this time is several thousand volts to tens of thousands of volts. How to measure the signal frequency in a high voltage environment? An oscilloscope as a general basic measuring instrument can cope with this situation. There are two ways to measure the oscillation frequency. One is the direct measurement method. The high-voltage attenuation probe is used to attenuate the signal and input into the oscilloscope for direct measurement. The other induction method is to use an ordinary passive probe to sense the electromagnetic field in a high-voltage environment. measuring. In the selection of measuring points, the induction method uses the passive probe as an inductive antenna. Under normal working conditions, the high-frequency electromagnetic field after oscillation can be generated in a certain range around the machine. The probe is in any position of the high-frequency electromagnetic field. Oscillation frequency measurement can be achieved. In terms of safety, the induction method does not need to directly touch the part of the machine circuit, just close the probe to the machine, and it will not cause harm to the machine and the human body. In terms of cost performance, since the direct measurement method requires an external high-voltage attenuation probe, the cost is much higher than the induction measurement. Therefore, it is the best choice to measure the oscillation frequency of the fusion splicer by induction.
Digital oscilloscopes have two methods for measuring signal frequency: software methods and hardware methods. The software method is that the software intercepts one of the calculated average periods in the waveform stored in the real-time memory of the oscilloscope, and then converts it into frequency. The frequency of the hardware method is measured by the hardware frequency meter. The hardware frequency meter will calculate the number of triggers per second of the trigger circuit as the frequency, so the signal should be guaranteed to be triggered. The software method and the hardware method are consistent when measuring the regular waveform, but there is a big difference between the measured values ​​of the irregular waveform. At this time, the value measured by the software method has lost its practical significance in constant changes. The hardware method The measured values ​​are more stable and closer to the average frequency and can be used as a reference. Moreover, when measuring the oscillation frequency, the accuracy is required to be high, and it needs to be accurate to 3 digits after the decimal point. The software measurement value is only 2 digits after the decimal point, and the hardware frequency meter can reach more than 3 digits. Due to the high frequency accuracy requirements, it is best to choose an oscilloscope that uses an active crystal. Since the general oscilloscopes are passive crystals configured, I chose the digital oscilloscope of the Dingyang SDS1000CFL series. The 6-bit real-time counting active crystal frequency meter fully meets the measurement accuracy requirements.
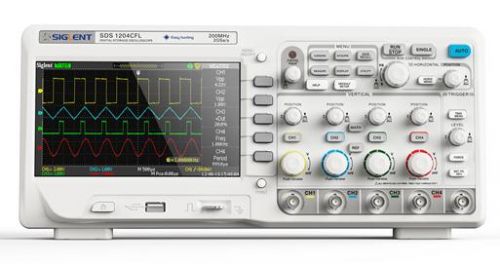
In the actual measurement, the author found that the signal noise interference is large, which leads to the hardware frequency meter display and the actual error. This requires the oscilloscope to have a good ability to filter and process noise. The SDS1000CFL has its unique digital filtering function (including low pass). , high pass, band pass, band stop), can effectively avoid false trigger caused by noise, making the measured value more accurate. The figure below shows the measured value obtained by the author using 1KHz, 40mV signal to simulate the interfered signal. It can be seen from the figure that the frequency measurement value after the digital filtering is turned on is consistent with the actual signal.
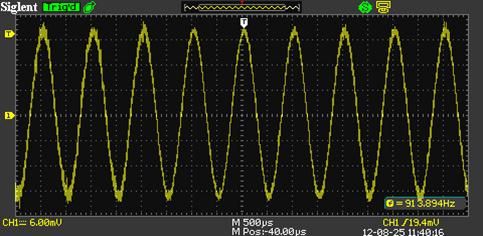
1KHz signal, measured value is 913.894Hz
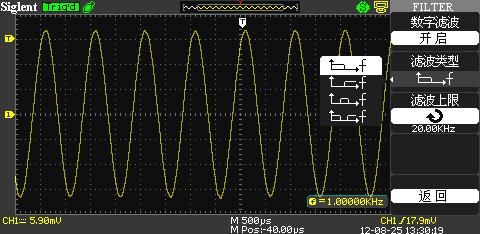
1KHz signal, digital filtering is turned on, the measured value is 1KHz
Inductive measurement is different from ordinary measurement. When the inductive method is used, the virtual probe is formed between the probe of the passive probe and the grounded alligator clip. When an electromagnetic field passes through the loop, it will generate induction electricity and pass it through the probe to the oscilloscope. Without grounding, separate the probe from the alligator clip to form a linear antenna or connect the probe to the alligator clip to form a loop antenna. In the normal measurement, the ground alligator clip needs to be grounded to avoid noise interference. Since only the frequency value needs to be measured, the operation steps are relatively simple. Firstly, the horizontal and vertical gear positions of the oscilloscope are adjusted to appropriate positions (multiple tests are required in advance), the digital filtering function is turned on, the probe senses the signal, and the hardware frequency meter reading is observed. Finally, record the optimal oscillation frequency of different products. In the production of the corresponding products, the oscillation frequency is first adjusted to the optimal reproduction, and the yield is improved.
The way the inductive method measures the oscillation frequency can be applied to other high frequency machines like the working principle, which is just a simple application of the oscilloscope. As the functionality increases and the accuracy increases, the oscilloscope will gain more applications and popularity in the field of test and measurement.
Automotive Connector 27P External Thread Assembly
Automotive Connector 27P External Thread Assembly
Automotive Connector 27P External Thread Assembly
ShenZhen Antenk Electronics Co,Ltd , https://www.atkconnectors.com